The steel grating produced by Hebei ZhenXing JinYuan Wire Mesh Group is crafted using world-class equipment from the Italian ORSOGRIL company, ensuring a product of exceptional quality and strength. This process involves arranging flat steel and twisted square steel in a precise longitude and latitude pattern at specific intervals. A key step in the manufacturing process is the use of a computer-controlled, high-voltage resistance welder that meticulously presses the twisted square steel into the flat steel. This advanced technique results in a robust solder joint, integral to the grating’s overall durability and structural integrity.
What sets our steel grating apart is its smooth surface and extremely high strength, attributable to the advanced Italian ORSOGRIL equipment. This equipment is capable of arranging the bearing bar (flat steel) and the cross bar (twisted square steel) in an orderly longitude and latitude fashion, at carefully measured distances. The critical process of welding, which is a high-tension resistance operation, is meticulously controlled by a computer system. This precision ensures that each grating produced meets our stringent standards of firm welding and smooth surface finish.
The result is a high-quality steel grating that not only boasts a flat, smooth surface but also demonstrates exceptional strength and durability. These qualities make our steel gratings ideal for a variety of applications, ranging from industrial flooring to architectural designs.
Most Popular Specifications of Steel Grating


Steel gratings with a bearing bar pitch of 30mm are the most widely used in the industrial field, offering the strongest resistance to surface impact. This type is ideal for areas subjected to heavy loads and frequent traffic.

The version with a 40mm bearing bar pitch is the lightest and most economical, making it the optimal choice for applications with small spans. Its lightweight nature allows for easy installation and maintenance.

For the mining industry, steel gratings with a bearing bar pitch of 60mm and a crossbar pitch of 50mm are specially designed. This configuration effectively prevents mineral splash, making it a common choice in mining processing plants.

The variant with a bearing bar pitch of 30mm and a crossbar pitch of 76mm is highly popular both domestically and internationally. It is versatile for various applications, including walkways and platforms.
Bearing Bar Types
Bearing bars in steel grating are categorized into four distinct types, each designed to cater to specific needs and applications:
Smooth Flat Steel Bar: This type features a flat, smooth surface, making it ideal for walking and moving equipment across. Its even surface provides stability and is commonly used in applications where ease of movement is crucial.
Serrated Toothed Bar: Equipped with a serrated, tooth-like pattern, this bar offers enhanced slip resistance. It is particularly suitable for environments where there is a potential for slippery conditions, such as in wet or oily areas.
Smooth I Bar: The Smooth I bar is characterized by its I-shaped cross-section, offering a unique combination of reduced weight and high strength. This design is often used in applications where both load-bearing capacity and material efficiency are important.
Serrated I Bar: Combining the I-shaped profile with a serrated surface, the Serrated I bar provides both the structural efficiency of an I bar and the added safety of slip resistance. This makes it an ideal choice for areas requiring both strength and safety underfoot, especially in challenging environmental conditions.
Each of these bearing bar types is designed to meet specific functional requirements, ensuring safety, durability, and efficiency in a variety of grating applications.

Plain Type

Serrated Type

I Type

Serrated I Type

Note:
- Bearing bar pitches are available in 15, 22, 25, 30, 32.5, 34, 40, 50, 60, 80, and 90mm, with 25, 30, 34, and 40mm being the recommended options.
- Crossbar pitches can range from 24 to 200mm, with 50, 76, and 100mm being the preferred choices.
- Bearing bar shapes:
F: Plain style (can be omitted in markings)
S: Serrated style
I: I-section style - Surface treatment options:
G: Hot dipped galvanized (can be omitted in markings)
P: Painted
U: Untreated
These specifications are designed to cater to a wide range of industrial and commercial needs, offering versatility, durability, and safety in various environments.
Surface Treatment of Steel Grating
Steel grating undergoes various surface treatments to enhance its durability and resistance to environmental elements. The primary methods include hot dip galvanizing and painting. These surface treatments not only extend the lifespan of steel grating but also ensure its performance in diverse applications, from industrial environments to architectural designs.

- Hot Dip Galvanizing: This process is typically performed post-edge wrapping, where the grating is submerged in molten zinc. For load-bearing bars with a thickness of at least 5mm, the average zinc layer weight after galvanizing is not less than 610g/m². For bars less than 5mm thick, this weight is not less than 460g/m². The quality of the galvanizing and the requirements comply with GB/T 13912 standards. Hot dip galvanizing adds a significant layer of protection against corrosion, making the steel grating suitable for a range of environmental conditions.
- Painting: Steel grating can also be coated with a protective layer through spraying, brushing, or dipping. This method is used to add an additional layer of protection against various elements and to provide aesthetic appeal to the grating.
- Service Life and Corrosion Resistance: The service life of hot dip galvanized steel grating is influenced by the thickness of the zinc coating, which is typically around 100 micrometers. In various environmental conditions, this coating significantly extends the product’s lifespan. Moreover, the zinc layer offers resistance to acid and alkali corrosion within a pH range of 6 to 12.5. A stable protective film forms on the zinc surface, enhancing the grating’s anti-corrosive properties.
Product aliases and Applications
- Hot-Dip Galvanized Grating: Often referred to as Hot-Dip Galvanized Grating, this variant undergoes a process where the grating is submerged in molten zinc, forming a thick, protective zinc coating. This method provides exceptional resistance to rust and corrosion, making it ideal for outdoor or harsh environmental conditions. The hot-dip galvanization ensures a long-lasting, durable finish.
- Zinc-Coated Steel Grating: Also known as Zinc-Coated Steel Grating, this type features a protective layer of zinc applied over the steel surface. The zinc coating acts as a barrier against moisture and environmental elements, extending the grating’s lifespan. This coating process is particularly effective for preventing rust, making it suitable for applications prone to moisture exposure.
- Galvanized Welded Steel Grating: Known as Galvanized Welded Steel Grating, this type emphasizes the welding process used to join the bars, followed by galvanization for corrosion resistance. The welding ensures structural integrity and strength, while the galvanization protects against environmental wear, making it suitable for heavy-duty applications.
- HDG Grating: Short for Hot-Dip Galvanized Grating, HDG Grating refers to the specific galvanization technique used. This process involves immersing the grating in molten zinc, creating a robust, protective coating. Ideal for extreme conditions, HDG Grating is celebrated for its longevity and resistance to harsh elements.
- Industrial Galvanized Grating: As Industrial Galvanized Grating, this variety highlights its application in industrial environments. The steel grating undergoes galvanization for durability and rust resistance, making it a steadfast choice for platforms, walkways, and drainage in industrial settings.
- Heavy-Duty Steel Grating: Heavy-Duty Steel Grating is designed to withstand extreme loads and high-traffic conditions. Manufactured with thicker bars and closer spacing, this type of grating provides enhanced strength and durability, making it ideal for industrial applications such as loading docks, truck and aircraft ramps, and large machinery areas. Its robust construction ensures longevity and reliability in environments where standard steel grating might not suffice. This grating is a preferred choice in sectors where safety and load-bearing capacity are critical, such as in heavy manufacturing, transportation infrastructure, and commercial facilities that handle heavy equipment.
How to Install Steel Grating
Installing steel grating involves two primary methods: welding and the use of mounting clips, each suitable for different applications.
- Welding Method: This approach is ideal for permanent fixtures where the grating will not require disassembly, such as around equipment platforms. The process involves angle welding at the first bearing bar of each corner of the grating. The welded seam should be no less than 20mm in length and 3mm in height to ensure stability and strength.
- Mounting Clips: For installations where disassembly might be necessary, or to avoid damaging the zinc layer of the grating, mounting clips are the preferred method. These clips are suitable for all types of steel grating and are composed of an upper clip, lower clip, and an M10 hexagonal cylindrical head bolt. When using mounting clips, at least four sets should be used per grating panel. For larger spans, it is advisable to use additional clips on available supports to enhance stability.
- Materials: To cater to different requirements, stainless steel mounting clips can be provided. These are particularly useful in environments where corrosion resistance is important.
- Ordering Mounting Clips: When ordering mounting clips, it’s essential to specify the type, quantity, and material required for your specific application.
- Installation Clearance: Ensure that there is adequate clearance during installation for the best fit and functionality of the grating.

Both welding and mounting clips offer effective solutions for installing steel grating, with the choice depending on the permanence of the installation and the need to preserve the grating’s protective coating.
See pictures for examples

Also known as Zinc-Coated Steel Grating, this type features a protective layer of zinc applied over the steel surface. The zinc coating acts as a barrier against moisture and environmental elements, extending the grating’s lifespan. This coating process is particularly effective for preventing rust, making it suitable for applications prone to moisture exposure.
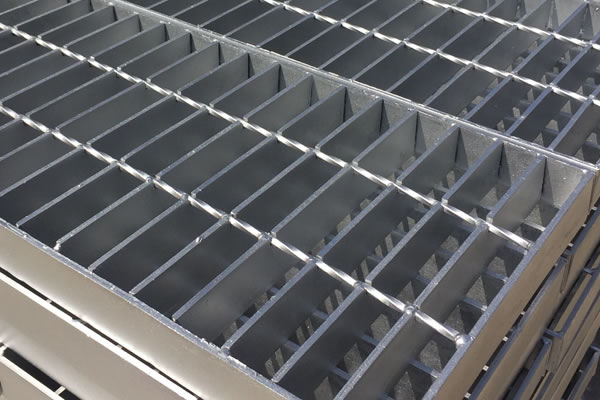
Often referred to as Hot-Dip Galvanized Grating, this variant undergoes a process where the grating is submerged in molten zinc, forming a thick, protective zinc coating. This method provides exceptional resistance to rust and corrosion, making it ideal for outdoor or harsh environmental conditions. The hot-dip galvanization ensures a long-lasting, durable finish.

Short for Hot-Dip Galvanized Grating, HDG Grating refers to the specific galvanization technique used. This process involves immersing the grating in molten zinc, creating a robust, protective coating. Ideal for extreme conditions, HDG Grating is celebrated for its longevity and resistance to harsh elements.

ZhenXing Jinyuan Welded Steel Grating, this type emphasizes the welding process used to join the bars, followed by galvanization for corrosion resistance. The welding ensures structural integrity and strength, while the galvanization protects against environmental wear, making it suitable for heavy-duty applications.