Hebei ZhenXing JinYuan Wire Mesh Group specializes in the manufacture and export of high-quality Fiberglass Reinforced Plastic (FRP) Grating products. These are designed to cater to the varied requirements of different industrial applications. Our product range includes Molded Fiberglass Grating and Pultruded FRP Grating. We are committed to providing FRP Grating products that are reliable, efficient, and customized to meet the specific needs of each application. Our focus on quality and customer satisfaction motivates us to constantly enhance and innovate our offerings, ensuring they adhere to the highest standards of performance and safety.
Molded Fiberglass Reinforced Plastic Grating
Our Molded FRP grating, known for its strength, durability, and exceptional corrosion resistance, is ideal for industries facing harsh conditions and environments prone to chemical exposure. This versatile material is widely used across various applications. In manufacturing, chemical plants, and refineries, it provides crucial corrosion resistance. It’s also perfect for outdoor or corrosive environments like marinas, water treatment plants, and offshore platforms, where it serves as durable walkways, footbridges, and trench covers. Additionally, its lightweight yet robust nature makes it suitable for architectural uses, such as facades and landscaping. In industrial settings, it offers a safe, non-slip surface for platforms, workstations, and drainage solutions. Molded FRP grating effectively combines safety and performance for a range of industrial and architectural needs.
Pultruded FRP Grating
Our Pultruded FRP Grating is tailored for high-strength and durability requirements, making it an ideal choice for various industrial settings. This grating’s unique manufacturing process allows it to withstand significant loads, perfect for walkways, platforms, and heavy-duty applications. Specifically, our FRP Walkway Grating is designed for safe and secure pedestrian paths, offering durability, corrosion resistance, and anti-slip properties. It is well-suited for industrial plants, commercial buildings, and other areas where pedestrian safety is paramount. Additionally, our Anti-Slip FRP Grating provides enhanced slip resistance, ensuring personnel safety in wet, oily, or slippery conditions. This versatility makes our grating products ideal for a wide array of applications, particularly where safety and heavy-load capacity are crucial. The Heavy-Duty Grating variant, with its thicker bars and more robust construction, is specifically designed for areas with high foot traffic or heavy loads.
Production Methods of FRP Grating
Fiberglass Reinforced Plastic (FRP) grating, renowned for its exceptional strength, durability, and corrosion resistance, is a versatile material widely used in various industries. The production of FRP grating primarily involves two principal methods – Molded and Pultruded – each tailored for specific applications and performance requirements. Additionally, a specialized method, Phenolic FRP Grating, caters to high-risk environments.
- Molded FRP Grating
Molded FRP Grating is a widely adopted method known for its versatility and effectiveness. This process starts with laying continuous strands of fiberglass in a mold. These strands are systematically layered and then covered with resin. Upon heating, the resin polymerizes and hardens, resulting in a robust and durable grating. This method’s flexibility allows for a variety of sizes, thicknesses, and mesh patterns, making it suitable for diverse applications. The high strength-to-weight ratio and excellent corrosion resistance of molded FRP grating make it a preferred choice for many industrial applications. - Pultruded FRP Grating
Pultruded FRP Grating, distinct from the molded approach, involves pulling continuous fiberglass strands through a resin bath, ensuring they are thoroughly coated with a resin mixture. These resin-infused fibers are then formed into the desired shape and passed through a heated die, where the resin solidifies, forming a strong structure. This method is notable for its high load-bearing capabilities and the ability to span greater distances compared to molded grating. Pultruded FRP grating is often utilized in scenarios requiring longer support spans, such as walkways and platforms in industrial settings. - Phenolic FRP Grating
Phenolic FRP Grating employs a process similar to the molded method but stands out due to its use of phenolic resin. This resin provides exceptional fire and smoke resistance, making phenolic FRP grating ideal for high-risk areas like offshore platforms, marine applications, and industries where fire safety is paramount. This method’s emphasis on safety without compromising on strength makes it a critical choice for specific, demanding environments.
The selection of the appropriate FRP grating production method hinges on various factors, including load-bearing capacity, fire resistance, environmental conditions, and cost considerations. While Molded and Pultruded FRP grating remain the most popular due to their balance of strength, cost-effectiveness, and adaptability, Phenolic FRP grating is an essential method for specialized applications demanding enhanced fire resistance. Each method is designed to meet distinct industrial requirements, ensuring that FRP grating continues to be a reliable and efficient solution across a broad spectrum of applications.
Commonly Used Surface Treatment Methods for FRP Grating
Fiberglass Reinforced Plastic (FRP) grating is a versatile material widely utilized in diverse applications. To enhance its properties for specific uses, its surface can undergo various treatments, each adding unique functional characteristics. These treatments enhance the grating’s suitability for a range of industrial and commercial applications.
- Solid Nosing: This involves adding a solid, often contrasting, strip at the edge of the grating steps, significantly improving visibility and safety. This method is particularly useful for anti-slip stairs in industrial or commercial settings, providing an additional safety measure.
- Concave Surface: The concave surface treatment creates a slightly indented pattern on the FRP grating. This basic level of anti-slip protection is suitable for general-purpose applications where moderate slip resistance is needed.
- Smooth Surface: Typically used for decorative purposes, a smooth surface finish is ideal for architectural elements like door partitions and ceilings. This finish emphasizes aesthetics over anti-slip properties.
- Solid-Covered Surface: Covering the grating with a solid layer enhances its anti-slip properties, prevents liquid leakage, and reduces the volatilization of gases and smoke. It’s an ideal choice for environments where spillage or emissions are a concern.
- Gritted Surface: Achieved by embedding fine particles into the top layer of the grating, a gritted surface offers excellent anti-slip properties. It is especially suitable for high-risk areas where maximum slip resistance is crucial.
- Micro/Mini Mesh Surface: This surface features a very fine mesh pattern, designed to prevent small tools and items from falling through the grating. It’s beneficial in industries where dropped tools or parts could create safety hazards or significant inconvenience.
- Additionally, specific coatings can be applied to further enhance the properties of FRP grating:
Anti-Slip Coating: Increases surface friction, reducing slips and falls.
UV Protection Coating: Prevents degradation from UV light, preserving color and integrity.
Chemical-Resistant Coating: Protects against corrosive substances.
Fire-Retardant Coating: Slows down fire spread and reduces smoke production.
Color Coating: Enhances visual appeal and aids in demarcation or safety signaling.
Sealant Coating: Seals surface pores, protecting against moisture and contaminants.
These surface treatments collectively ensure the functionality, safety, durability, and suitability of FRP grating for various environments, making it a highly adaptable and reliable material choice.
General Specifications of FRP Grating
Hebei ZhenXing JinYuan Wire Mesh Group offers a diverse range of FRP Grating products, including both molded and pultruded varieties, to meet a broad spectrum of industrial needs. Available in a wide array of sizes and specifications, these products are suitable for a variety of applications, from extensive industrial platforms to compact walkways. Our commitment to offering detailed specifications and customization options ensures that our high-quality FRP Grating products meet the specific requirements of your industrial or commercial projects precisely.
- Length & Width: Our FRP Grating is available in lengths ranging from 1 meter to 10 meters, and widths between 0.5 meters to 2 meters. This range allows for flexible adaptation to different spaces, ensuring a seamless fit for various project layouts.
- Thickness: The thickness of our grating varies from 25mm to 50mm, catering to different load-bearing and durability requirements. Thicker grating is typically used for areas with heavier loads, while thinner grating is sufficient for lighter applications.
- Mesh Size: We offer a variety of mesh sizes, from small meshes of 13mm x 13mm for fine applications, up to standard sizes of 38mm x 38mm. The smaller mesh sizes are ideal for preventing small objects from falling through, whereas larger meshes are suitable for more general applications.
- Color Options: Our grating is available in a spectrum of colors, ranging from standard industrial hues to more vibrant options. These color choices not only enhance the aesthetic appeal of the installations but also can be used for safety and zoning purposes in different industrial settings.
- Load Bearing Capacity: Our products are engineered to support loads from 500 kg/m² up to 5000 kg/m², making them versatile for both light and heavy-duty applications. This range ensures that our grating can safely accommodate the needs of various industrial environments.
- Customization: Understanding the unique nature of each project, we offer custom sizes, colors, and load capacities. Whether it’s a specific color to match your company’s branding or a unique size for a specific area, our customization options ensure that your exact needs are met.
See pictures for examples

Known as Fiberglass Reinforced Plastic Grating, this type emphasizes its composition of fiberglass and resin, offering high strength and corrosion resistance. It’s ideal for harsh chemical environments and areas requiring lightweight yet durable materials, such as industrial platforms and walkways.

Composite Grating, highlighting its mixed material construction, combines the strength of fiberglass with the flexibility of plastic. This combination makes it resistant to both corrosion and impact, suitable for diverse applications ranging from industrial flooring to pedestrian bridges.

Non-Conductive Grating, as the name suggests, is designed to be electrically non-conductive, making it ideal for electrically sensitive environments like power plants and telecommunications facilities. Its insulating properties add an extra layer of safety in such settings.
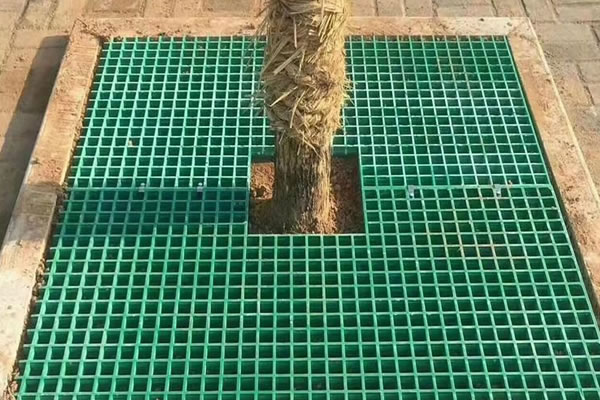
Anti-Corrosive FRP Grating emphasizes its resistance to corrosive substances, making it ideal for chemical plants, coastal areas, and other corrosive environments. Its ability to withstand harsh chemicals without degrading ensures longevity and reliability in challenging settings.